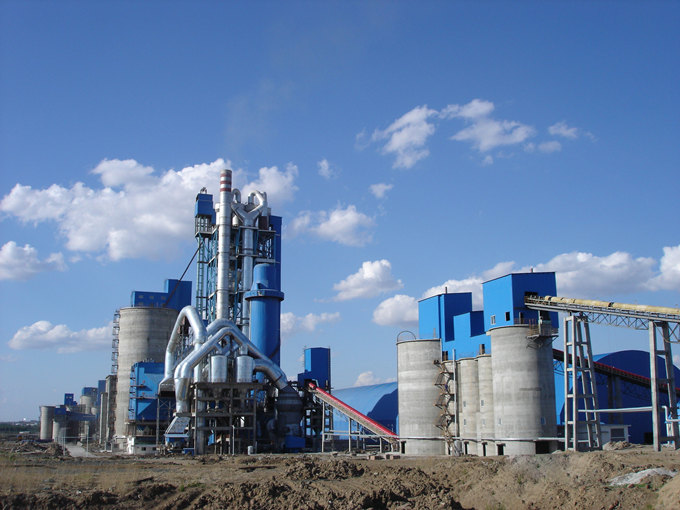
技术介绍
当前我国正处于工业化、城镇化加速发展的重要阶段,经济社会发展面临着严峻的资源和环境双重约束。水泥行业作为我国主要的高能耗、高排放产业,是工业领域节能减排的重点和难点,其节能减排效果对完成我国能源消耗目标和工业可持续发展起着举足轻重的作用。据国家发改委《节能中长期专项规划》指出,我国水泥单产综合能耗比国际先进水平高45.3%,差距明显。因此,在水泥行业推广优化控制技术,推行清洁生产,降低综合能耗,减少污染物排放,实现绿色发展,对于促进水泥全行业的技术进步,具有十分重要的意义。
在水泥企业面向节能降耗自动化、信息化改造方面,我公司结合常年现场经验、反复试验,开发出具有自主知识产权的水泥生产节能优化控制系统和水泥生产能效与分析管理系统。在实际应用中,为企业节能降耗创造了巨大的收益。
水泥生产节能优化控制系统
水泥生产节能优化控制系统旨在解决水泥生产的自动控制与过程优化难题。结合企业现状,最大程度提高企业的自动化程度及节能降耗水平,以达到无人值守及节能减排的目的。本系统由熟料烧成过程优化、生料质量控制及粉磨负荷优化三部分核心技术组成,在保证水泥生产三大工序(生料制备、熟料烧成、水泥制备)稳定控制的基础之上,对水泥生产的全流程进行优化,实现企业的稳产、增效、节能、降耗。
优化后可实现主要生产数据:
以某日产5000吨熟料的应用示范线为例,通过统计数据对比,系统投运后,
节煤:2.27公斤煤/吨熟料 * 150万吨熟料/年=3405吨
年可创经济效益:620元/吨煤*3405吨煤= 211万元。
系统总体架构
本优化控制系统最大特点是立足水泥企业现状,无需对现有工艺及测控设备进行改造。只需要要在原有DCS配有OPC接口的基础上,通过工业控制技术和优化控制即可实现水泥生产的全流程自动控制与过程优化。系统综合运用了各类检测技术及控制技术,并结合了人工操作经验与先进控制算法,是3C(控制、计算机、通信)技术最新成果在水泥控制领域的集中体现。
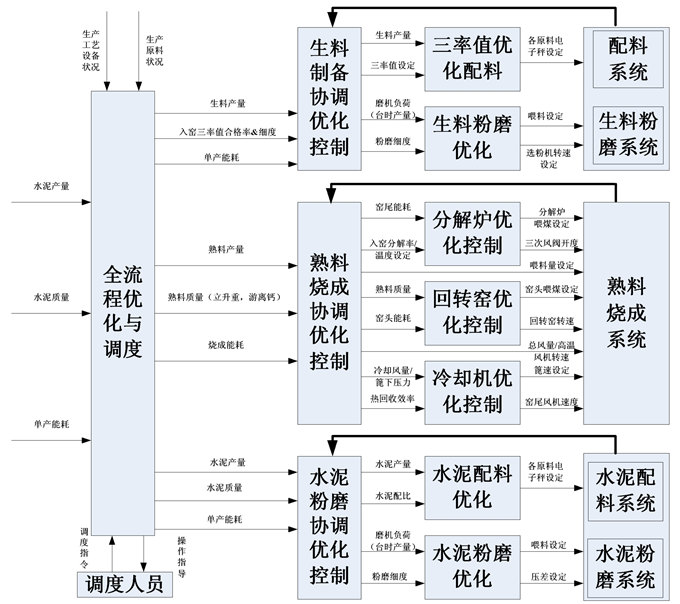
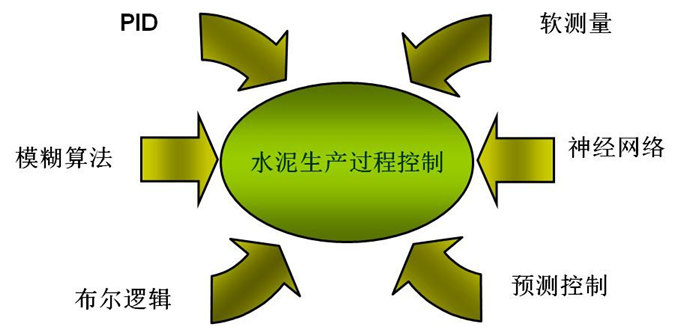
1、熟料烧成过程节能优化
水泥熟料烧成过程作为水泥生产的核心环节,决定了整个生产过程的产量与质量,也基本决定了水泥生产的单产煤耗。

主要控制目标v 分解炉温度稳定
v 烧成带温度(软测量值)稳定
v 窑头负压稳定
v 篦下压力稳定
v 其他(小仓仓重、入窑生料量、煤磨出口温度等)
主要优化目标
v 保质、保产前提下使得熟料烧成综合能耗最小
控制难点:
v 关键参数(分解炉、烧成带温度等)不能直接测量
v 原燃料成分、设备状态多变
v 系统变量多、控制参数滞后
使用的手段和算法:
v 采用先稳定、后优化的控制策略
v 综合运用变速积分PID、FUZZY控制、Bang-Bang控制、多模态智能控制及预测控制算法实现烧成过程各关
键工艺参数稳定
v 通过热效在线计算对控制参数进行优化设定
v 通过使用法国HGH高温探测仪(建议用户购买),可以更加准确实时的显示炉内温度烧成自动控制与过程
优化:先稳定、后优化
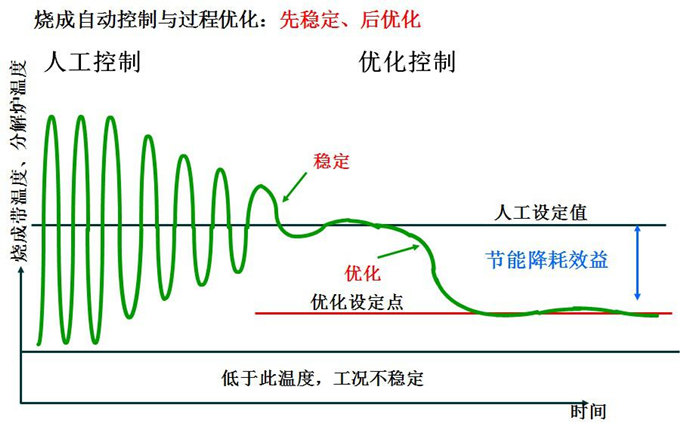
实现效益:
v 显著提高水泥熟料生产过程运行的稳定性和安全性
v 改变长期处于人工操作、轮班带来的生产波动
v 使F-CAO接近最佳值,提高熟料产品质量
v 延长窑炉的连续运行周期,提高产能
v 节能降耗,综合煤耗降低,使水泥熟料烧成单产煤耗降低1-5%。
v 极大的减少了劳动量,自控率达80%以上。
应用效果示例
下图为某水泥厂真实效果图
人工控制时,分解炉波动范围约为860℃ - 900℃(相差40度,上图虚竖线(基本在中间的那条虚竖线)以左部分),投入优化控制系统后,分解炉温度波动范围下降为50℃,优化控制系统使分解炉的温度波动范围大大减小,使整个窑系统的工况更加稳定。
篦冷机篦速实际优化控制效果显示界面
通过优化控制篦速来稳定篦压,从而使二次风温稳定,进而使整个窑系统更加稳定。人工控制篦压的范围约在3500pa-4400pa(约900pa),自动控制篦压的范围约在3700pa-4200pa(波动500pa)。人工控制下二次风温波动范围约为1020pa-1120pa,自动控制下,二次风温波动范围约为1080pa-1150pa。
2、生料质量控制系统
生料质量控制是保证熟料质量以及最初水泥质量的前提。生料质量控制优化子系统基于在线或非在线成分分析仪的数据,根据各类原材料波动工况,自动选择最优配比调节方案,进而实现生料质量控制。
系统功能:
² v稳定生料成分
自动适应原料波动的多种工况,确保出磨生料成分稳定;
² v在线实时调整生料配比
若与在线全元素分析仪配合(我公司已与ABB及南非矿业达成合作协议),可全自动追踪原料的化学成分变化并实时调整配比,极大程度提高生料质量;
² v满足多种工艺
多种调整模式及策略,可以满足不同工艺条件下的配料要求;
3、粉磨负荷节能优化系统
粉磨过程是水泥生产的重要环节,本优化子系统实质上是一个在专家系统监督指导下的多变量控制系统。专家系统主要是根据现场实时参数和操作员经验来识别磨况,并协调粗、细粉仓的负荷,实现负荷优化,可节电1-3% 。
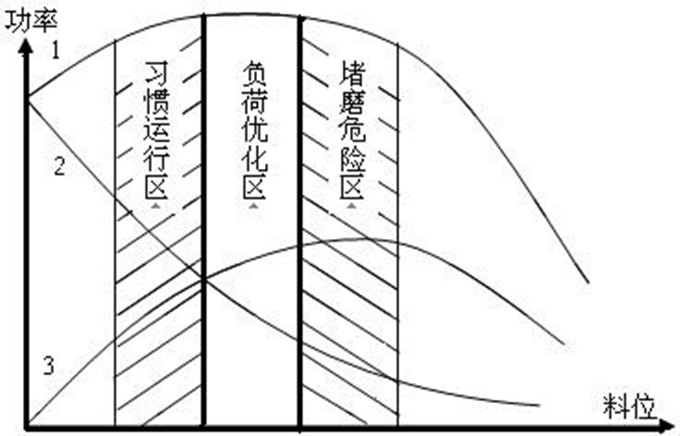
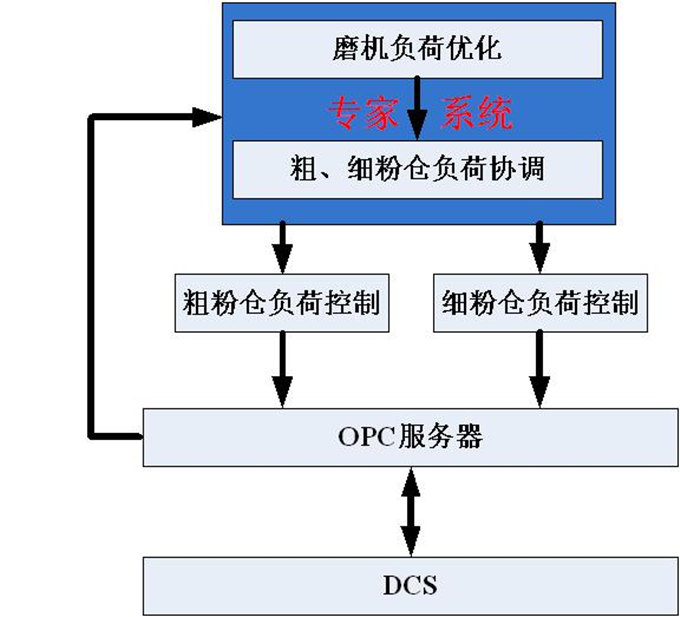
系统功能:
l v稳定的产品质量
水泥磨机荷载的持续监控以及装料和分离器的调整减少了水泥等级的多样性。使得产品质量更稳定,控制策略的目的在于对过程中的干扰因素做出反应,实现质量的确定性。
l v增加输出量
通过持续监控水泥磨机的荷载以及系统中材料流的平衡,可以识别何时给水泥磨机装料输出量会增加。观察证实,优化控制的水泥磨机可以长期增加输出量。
l v减少功率消耗
实现这一重要节省的原因是,优化控制的窑生成的渣块更软。此控制策略能够最佳地利用可用水泥磨机容量,并提高生产率。
l v降低研磨介质的消耗
因为优化控制的窑生成的渣块更软,所以研磨介质的消耗量减少了。
粉磨优化软件示例
当前我国正处于工业化、城镇化加速发展的重要阶段,经济社会发展面临着严峻的资源和环境双重约束。水泥行业作为我国主要的高能耗、高排放产业,是工业领域节能减排的重点和难点,其节能减排效果对完成我国能源消耗目标和工业可持续发展起着举足轻重的作用。据国家发改委《节能中长期专项规划》指出,我国水泥单产综合能耗比国际先进水平高45.3%,差距明显。因此,在水泥行业推广优化控制技术,推行清洁生产,降低综合能耗,减少污染物排放,实现绿色发展,对于促进水泥全行业的技术进步,具有十分重要的意义。
在水泥企业面向节能降耗自动化、信息化改造方面,我公司结合常年现场经验、反复试验,开发出具有自主知识产权的水泥生产节能优化控制系统和水泥生产能效与分析管理系统。在实际应用中,为企业节能降耗创造了巨大的收益。
水泥生产节能优化控制系统
水泥生产节能优化控制系统旨在解决水泥生产的自动控制与过程优化难题。结合企业现状,最大程度提高企业的自动化程度及节能降耗水平,以达到无人值守及节能减排的目的。本系统由熟料烧成过程优化、生料质量控制及粉磨负荷优化三部分核心技术组成,在保证水泥生产三大工序(生料制备、熟料烧成、水泥制备)稳定控制的基础之上,对水泥生产的全流程进行优化,实现企业的稳产、增效、节能、降耗。
优化后可实现主要生产数据:
以某日产5000吨熟料的应用示范线为例,通过统计数据对比,系统投运后,
节煤:2.27公斤煤/吨熟料 * 150万吨熟料/年=3405吨
年可创经济效益:620元/吨煤*3405吨煤= 211万元。
系统总体架构
本优化控制系统最大特点是立足水泥企业现状,无需对现有工艺及测控设备进行改造。只需要要在原有DCS配有OPC接口的基础上,通过工业控制技术和优化控制即可实现水泥生产的全流程自动控制与过程优化。系统综合运用了各类检测技术及控制技术,并结合了人工操作经验与先进控制算法,是3C(控制、计算机、通信)技术最新成果在水泥控制领域的集中体现。
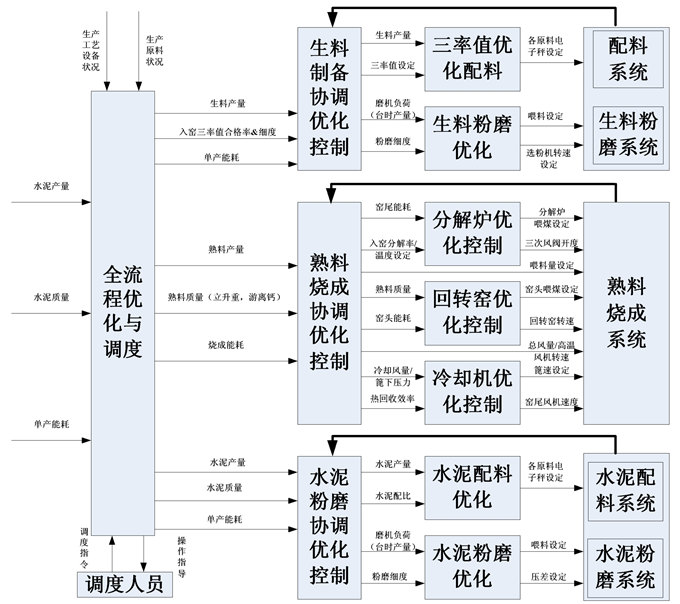
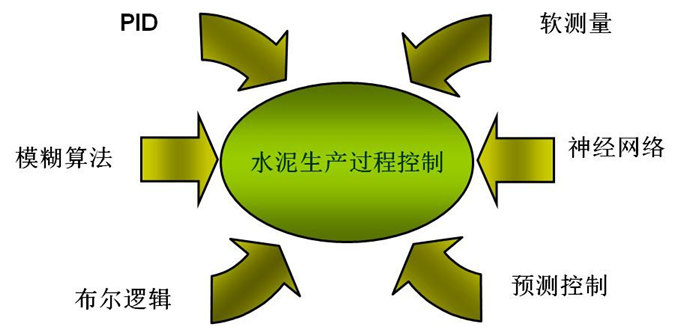
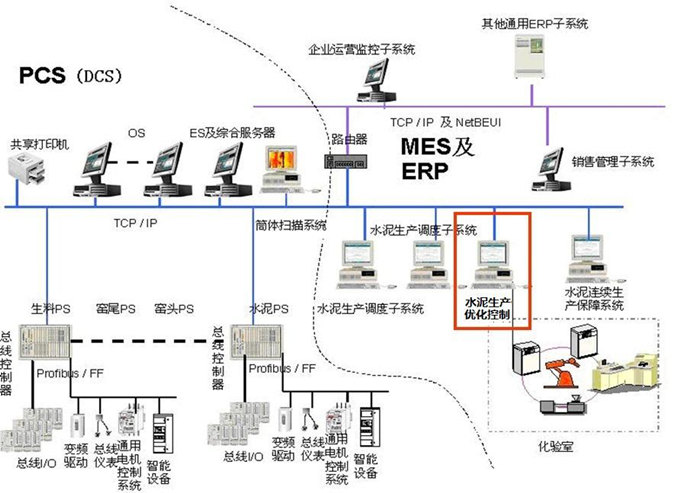
1、熟料烧成过程节能优化
水泥熟料烧成过程作为水泥生产的核心环节,决定了整个生产过程的产量与质量,也基本决定了水泥生产的单产煤耗。

主要控制目标v 分解炉温度稳定
v 烧成带温度(软测量值)稳定
v 窑头负压稳定
v 篦下压力稳定
v 其他(小仓仓重、入窑生料量、煤磨出口温度等)
主要优化目标
v 保质、保产前提下使得熟料烧成综合能耗最小
控制难点:
v 关键参数(分解炉、烧成带温度等)不能直接测量
v 原燃料成分、设备状态多变
v 系统变量多、控制参数滞后
使用的手段和算法:
v 采用先稳定、后优化的控制策略
v 综合运用变速积分PID、FUZZY控制、Bang-Bang控制、多模态智能控制及预测控制算法实现烧成过程各关
键工艺参数稳定
v 通过热效在线计算对控制参数进行优化设定
v 通过使用法国HGH高温探测仪(建议用户购买),可以更加准确实时的显示炉内温度烧成自动控制与过程
优化:先稳定、后优化
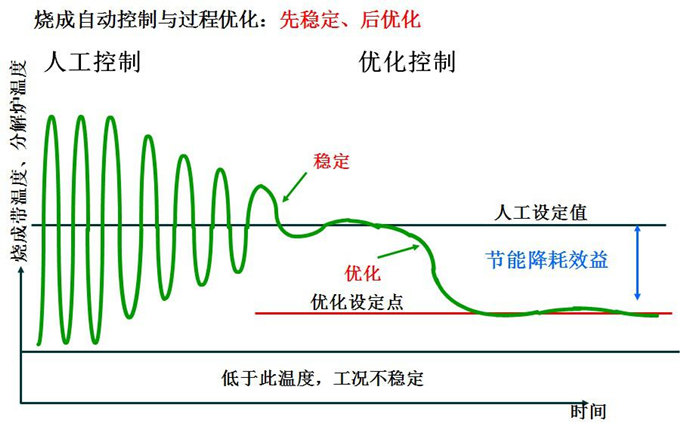
实现效益:
v 显著提高水泥熟料生产过程运行的稳定性和安全性
v 改变长期处于人工操作、轮班带来的生产波动
v 使F-CAO接近最佳值,提高熟料产品质量
v 延长窑炉的连续运行周期,提高产能
v 节能降耗,综合煤耗降低,使水泥熟料烧成单产煤耗降低1-5%。
v 极大的减少了劳动量,自控率达80%以上。
应用效果示例
下图为某水泥厂真实效果图
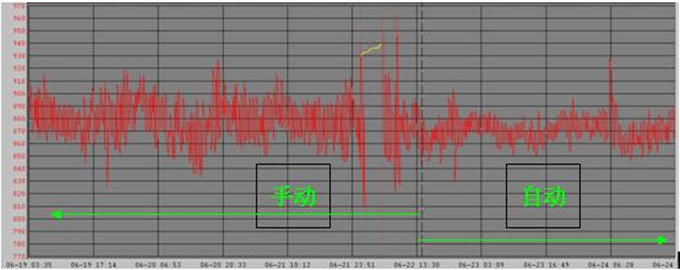
人工控制时,分解炉波动范围约为860℃ - 900℃(相差40度,上图虚竖线(基本在中间的那条虚竖线)以左部分),投入优化控制系统后,分解炉温度波动范围下降为50℃,优化控制系统使分解炉的温度波动范围大大减小,使整个窑系统的工况更加稳定。
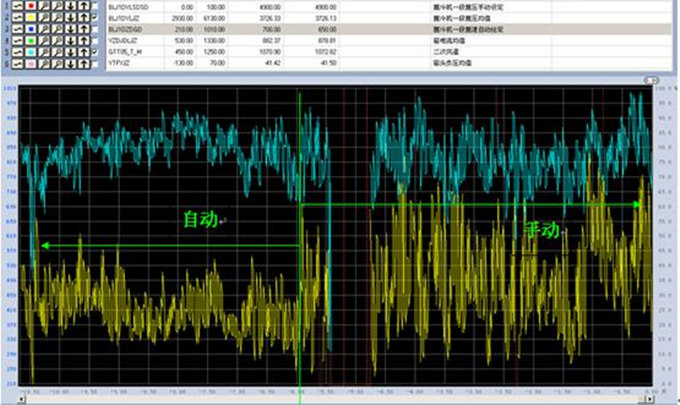
通过优化控制篦速来稳定篦压,从而使二次风温稳定,进而使整个窑系统更加稳定。人工控制篦压的范围约在3500pa-4400pa(约900pa),自动控制篦压的范围约在3700pa-4200pa(波动500pa)。人工控制下二次风温波动范围约为1020pa-1120pa,自动控制下,二次风温波动范围约为1080pa-1150pa。
2、生料质量控制系统
生料质量控制是保证熟料质量以及最初水泥质量的前提。生料质量控制优化子系统基于在线或非在线成分分析仪的数据,根据各类原材料波动工况,自动选择最优配比调节方案,进而实现生料质量控制。
系统功能:
² v稳定生料成分
自动适应原料波动的多种工况,确保出磨生料成分稳定;
² v在线实时调整生料配比
若与在线全元素分析仪配合(我公司已与ABB及南非矿业达成合作协议),可全自动追踪原料的化学成分变化并实时调整配比,极大程度提高生料质量;
² v满足多种工艺
多种调整模式及策略,可以满足不同工艺条件下的配料要求;
3、粉磨负荷节能优化系统
粉磨过程是水泥生产的重要环节,本优化子系统实质上是一个在专家系统监督指导下的多变量控制系统。专家系统主要是根据现场实时参数和操作员经验来识别磨况,并协调粗、细粉仓的负荷,实现负荷优化,可节电1-3% 。
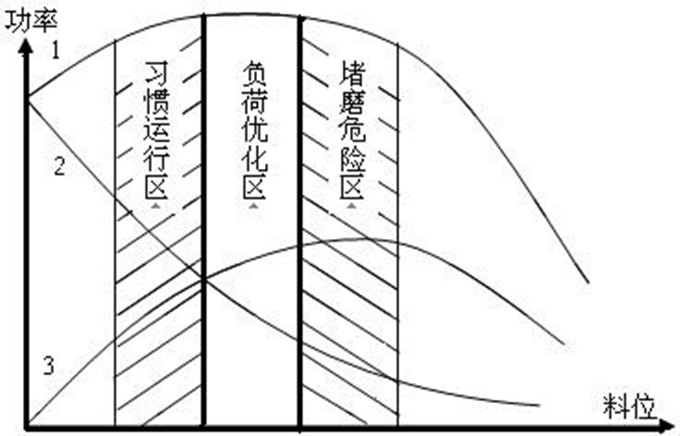
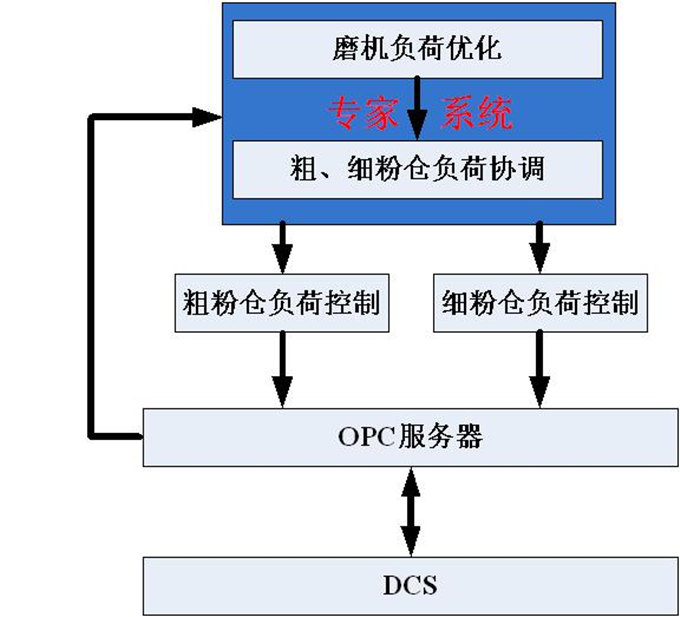
系统功能:
l v稳定的产品质量
水泥磨机荷载的持续监控以及装料和分离器的调整减少了水泥等级的多样性。使得产品质量更稳定,控制策略的目的在于对过程中的干扰因素做出反应,实现质量的确定性。
l v增加输出量
通过持续监控水泥磨机的荷载以及系统中材料流的平衡,可以识别何时给水泥磨机装料输出量会增加。观察证实,优化控制的水泥磨机可以长期增加输出量。
l v减少功率消耗
实现这一重要节省的原因是,优化控制的窑生成的渣块更软。此控制策略能够最佳地利用可用水泥磨机容量,并提高生产率。
l v降低研磨介质的消耗
因为优化控制的窑生成的渣块更软,所以研磨介质的消耗量减少了。
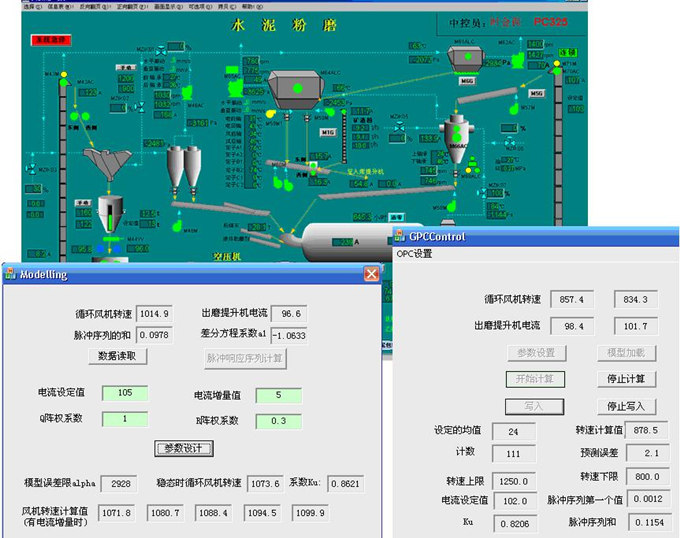